Facilities Management employs new process to improve chilling
May 1, 2013
Facilities Management has made strides to eliminate uncomfortably warm indoor temperatures, typical of this transitional time of year, by initiating chiller start-up early. With the early jump, chillers across campus are primed and on standby, ready to provide air conditioning to campus buildings.
Preparing the system three weeks ahead of the regular schedule is a direct result of being caught off guard by an unseasonable warm spring last year. Not having the chiller prepared lead to uncomfortably high indoor temperatures. It wasn't a scenerio the Division was looking to repeat. However, having the chillers online early comes with risks.
“There are reasons we haven’t started the chillers this early in the past,” says Gary Bridgens, Director, Facilities Management. “The process required precise coordination with the variable Spring temperatures, when extremes are capable of damaging the chilled water equipment.
Unlike at home, changing from heating to cooling requires much more planning and preparation than flipping a thermostat switch. With more than 90 buildings and millions of square feet of occupied space, the campus system can take more than three weeks to prime for start-up.
The majority of the preparation time is spent filling the coils that are emptied in the fall to prevent winter freezing. Although time consuming, it is a critical procedure. If outdoor temperatures dip below freezing the coils are subject to freezing, swelling, and splitting. As temperatures warm, the system thaws and leaks, rendering the equipment useless until repairs can be made.
“Keeping the delicate balance of comfortable indoor air temperatures and finding that sweet spot when we can safely start up the chillers has always been a challenge,” says Bridgens. “Current technology is allowing us to ease some of that timing pressure through the use of anti-freezing measures.”
With an automated pumping system, the coils can now be filled sooner. This year, fitters began filling coils three weeks earlier than in previous years. Should outdoor temperatures dip below five degrees Celsius, the system triggers the pumps to push water through the coils. Because moving water has a lower freezing point the pipes will remain open until the temperatures return to normal.
“There is still a risk of damage if the temperature sensing mechanisms or the pumps fail, however, we believe our customers will appreciate the enhancements we’ve made to have air conditioning ready earlier and that the potential benefits outweigh the risk involved,” says Bridgens.
Though these proactive measures will help to reduce temperature fluctuations in most buildings, it should be noted that irregular indoor temperatures are inevitable throughout the changing season. The campus community is encouraged to contact Facilities Management and report conditions that fall outside of acceptable standards for extended periods of time.
“We’d like to think that we will stop all irregularities by being ahead of the game,” says Bridgens. “That’s just not realistic, so we are still asking our customers to dress appropriately and expect brief periods of fluctuation.”
As always, the Division remains committed to enhancing service delivery at every level and continues to make the campus a more comfortable environment in which to work, study and research.
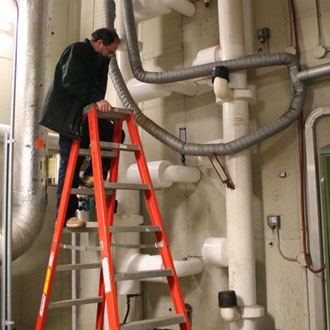
How air conditioning
works at Western
Cold water is used to cool the indoor air at Western. Giant chillers located in Natural Science and the Power Plant, super cool water and then circulate it across campus through an underground loop of pipe. The water is pumped up to coils, similar to radiator fins, in each of the buildings on campus. Air is forced between the coils, cooling the air, and is then directed into the occupied space as air conditioning. Water returns from the coils to the chillers, is super cooled and sent back out again.
Most of the residences and select satellite buildings are chilled with smaller satellite units.
It is a seemingly simple system, until you take into account the size of the campus.
• Number of chillers = 8*
• Volume of chilled water = 1,100,000 litres
• Number of coils = 108
• Space being cooled = 9+ million sq. ft.
* Not including small 'satellite' chillers located in buildings that are not on the chilled water loop.